A Breakthrough Could Revolutionize the Way We Refine Fuels and Store Hydrogen
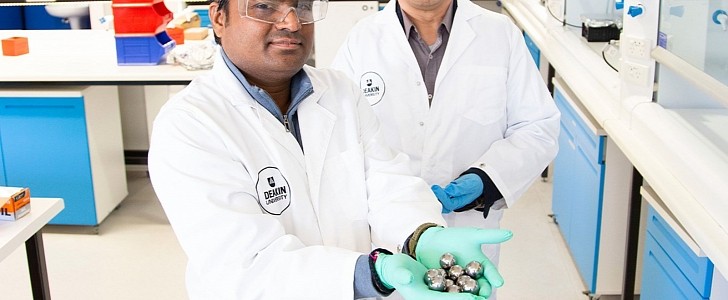
A team of researchers at Deakin’s Institute for Frontier Materials (IFM) found a new way of storing hydrogen, which is neither dangerous nor expensive. Like many other discoveries, it was done by accident. The team wanted to study a mechanochemical method to separate and store gases that could replace the energy-consuming cryogenic distillation processes in oil refineries. For that, they used boron nitride powder, a chemically safe material with rather interesting quality of absorbing gases in certain conditions.
The method involves grinding boron nitride powder with small stainless-steel balls inside a sealed chamber, a process both energy efficient and clean. As the chamber rotates at higher speeds, the pressure exerted by the steel balls on the powder increases until the conditions for the absorption of a certain gas are met. Each gaseous substance becomes adsorbed into the boron nitride powder at a specific pressure, so the gases are separated depending on the rotational speed of the sealed chamber.
The method was published in Materials Today, noting that the process requires only 10% of the energy spent in refineries to separate gases using the traditional cryogenic distillation process. This is huge, considering that refining fossil fuels accounts for 15% of all world’s energy usage. Other advantages are that the boron nitride powder can be reused multiple times and is a clean material, perfectly safe to keep in your household.
The team is confident that the same method can be used to store hydrogen inside the boron nitride powder. This could solve a significant problem that prevents wider hydrogen adoption. To release the hydrogen for later use (or any other gas for that matter), the powder simply needs to be heated at several hundred degrees Celsius in a vacuum.
“There’s a mechanochemical alternative [to traditional hydrogen storage], using ball milling to store gas in the nanomaterial at room temperature,” said Professor Ying (Ian) Chen, IFM’s Chair of Nanotechnology and co-author of the study. “It doesn’t require high pressure or low temperatures, so it would offer a much cheaper and safer way to develop things like hydrogen-powered vehicles.”
For now, this method is only a proof of concept, although it shows promising results. The team used the technique to separate only around 2-3 liters of material. Still, they are confident it can be scaled up for pilot production.