Researchers demo new type of carbon nanotube yarn that harvests mechanical energy
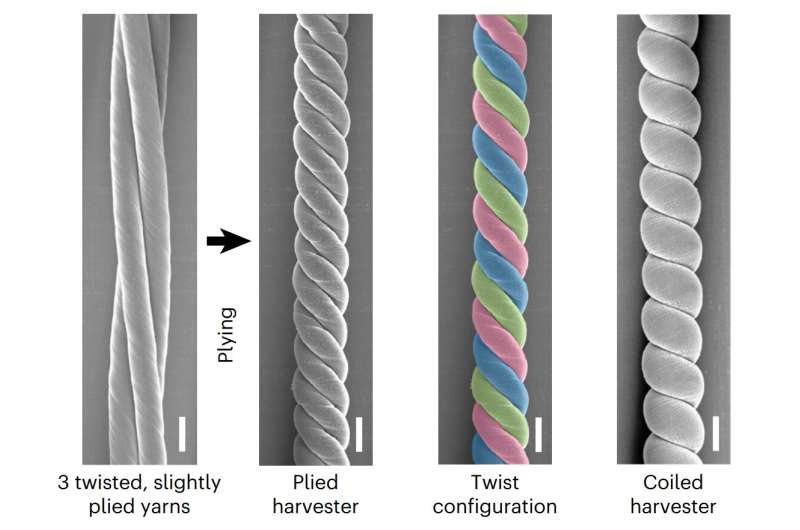
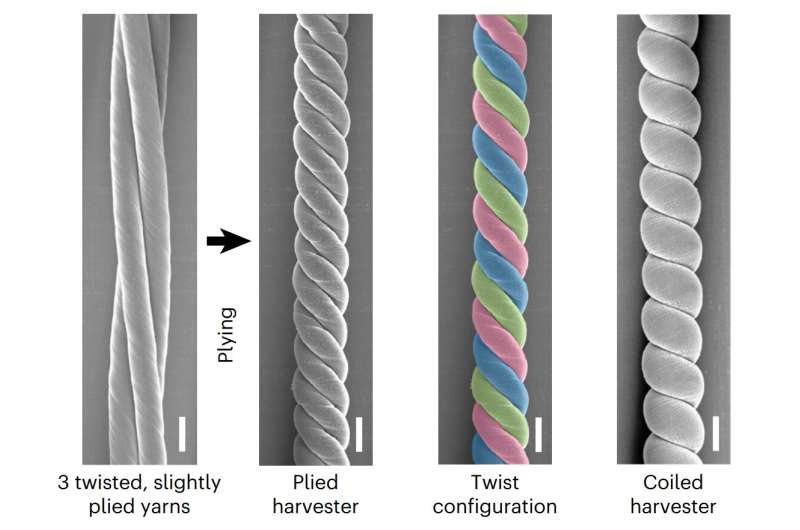
Nanotechnology researchers at The University of Texas at Dallas have made novel carbon nanotube yarns that convert mechanical movement into electricity more effectively than other material-based energy harvesters.
In a study published Jan. 26 in Nature Energy, UT Dallas researchers and their collaborators describe improvements to high-tech yarns they invented called “twistrons,” which generate electricity when stretched or twisted. Their new version is constructed much like traditional wool or cotton yarns.
Twistrons sewn into textiles can sense and harvest human motion; when deployed in salt water, twistrons can harvest energy from the movement of ocean waves; and twistrons can even charge supercapacitors.
First described by UTD researchers in a study published in 2017 in the journal Science, twistrons are constructed from carbon nanotubes (CNTs), which are hollow cylinders of carbon 10,000 times smaller in diameter than a human hair. To make twistrons, the nanotubes are twist-spun into high-strength, lightweight fibers, or yarns, into which electrolytes can also be incorporated.
Previous versions of twistrons were highly elastic, which the researchers accomplished by introducing so much twist that the yarns coil like an overtwisted rubber band. Electricity is generated by the coiled yarns by repeatedly stretching and releasing them, or by twisting and untwisting them.
In the new study, the research team did not twist the fibers to the point of coiling. Instead, they intertwined three individual strands of spun carbon nanotube fibers to make a single yarn, similar to the way conventional yarns used in textiles are constructed—but with a different twist.
“Plied yarns used in textiles typically are made with individual strands that are twisted in one direction and then are plied together in the opposite direction to make the final yarn. This heterochiral construction provides stability against untwisting,” said Dr. Ray Baughman, director of the Alan G. MacDiarmid NanoTech Institute at UT Dallas and the corresponding author of the study.
“In contrast, our highest-performance carbon-nanotube-plied twistrons have the same-handedness of twist and plying—they are homochiral rather than heterochiral,” said Baughman, the Robert A. Welch Distinguished Chair in Chemistry in the School of Natural Sciences and Mathematics.
In experiments with the plied CNT yarns, the researchers demonstrated an energy conversion efficiency of 17.4% for tensile (stretching) energy harvesting and 22.4% for torsional (twisting) energy harvesting. Previous versions of their coiled twistrons reached a peak energy conversion efficiency of 7.6% for both tensile and torsional energy harvesting.
“These twistrons have a higher power output per harvester weight over a wide frequency range—between 2 Hz and 120 Hz—than previously reported for any non-twistron, material-based mechanical energy harvester,” Baughman said.
Baughman said the improved performance of the plied twistrons results from the lateral compression of the yarn upon stretching or twisting. This process brings the plies in contact with one another in a way that affects the electrical properties of the yarn.
“Our materials do something very unusual,” Baughman said. “When you stretch them, instead of becoming less dense, they become more dense. This densification pushes the carbon nanotubes closer together and contributes to their energy-harvesting ability. We have a large team of theorists and experimentalists trying to understand more completely why we get such good results.”
The researchers found that constructing the yarn from three plies provided the optimal performance.
The team conducted several proof-of-concept experiments using three-ply twistrons. In one demonstration they simulated the generation of electricity from ocean waves by attaching a three-ply twistron between a balloon and the bottom of an aquarium filled with salt water. They also arranged multiple plied twistrons in an array weighing only 3.2 milligrams and repeatedly stretched them to charge a supercapacitor, which then had enough energy to power five small light-emitting diodes, a digital watch and a digital humidity/temperature sensor.
The team also sewed the CNT yarns into a cotton fabric patch that was then wrapped around a person’s elbow. Electrical signals were generated as the person repeatedly bent their elbow, demonstrating the potential use of the fibers for sensing and harvesting human motion.
The researchers have applied for a patent based on the technology.
More information:
Ray Baughman, Mechanical energy harvesters with tensile efficiency of 17.4% and torsional efficiency of 22.4% based on homochirally plied carbon nanotube yarns, Nature Energy (2023). DOI: 10.1038/s41560-022-01191-7. www.nature.com/articles/s41560-022-01191-7
Citation:
Researchers demo new type of carbon nanotube yarn that harvests mechanical energy (2023, January 26)
retrieved 26 January 2023
from https://techxplore.com/news/2023-01-demo-carbon-nanotube-yarn-harvests.html
This document is subject to copyright. Apart from any fair dealing for the purpose of private study or research, no
part may be reproduced without the written permission. The content is provided for information purposes only.