Why ISO 9001:2015 Certification Matters
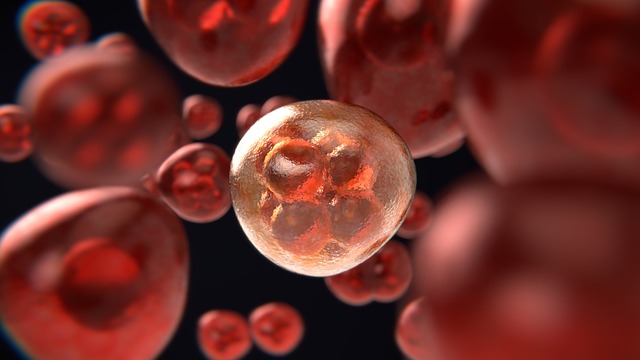
Establishing customer trust is essential for success in biotech and life sciences research, doubly so when operating in international markets. In many ways, this is easier said than done. Companies must carefully navigate the requirements of regulatory bodies while adapting their messaging to different cultural standards and market pressures.
Fortunately, demonstrating a dedication to thorough quality management practices is much more straightforward. Companies can do so by getting ISO 9001:2015 certified.
Headquartered out of Switzerland, the International Organization for Standardization (ISO) is an independent organization dedicated to standards development. ISO 9000:2015 certification is not performed by ISO, however. Instead, audits are conducted by outside agencies who are themselves carefully vetted.
To be ISO 9001:2015 certified, auditors must review the organizational structure, assess employees, and inspect processes[1]. Organizational efficiency, safety, and QMS processes are assessed at every level of a company. Classically, these inspections were performed in person, but the COVID-19 pandemic has required the adoption of virtual auditing for specific processes and situations.
A key benefit of being ISO 9001:2015 certified is that implementation of the required QMS procedures improves the quality of products, services delivered, and the customer experience. ISO 9001:2015 certification requires producing and maintaining records of product specifications and test results, ensuring accountability that drives better performance. Moreover, certification entails establishing a transparent line of communication with clients about expectations regarding service. By improving and ensuring the highest degree of quality standards, companies can engender client trust and may help justify the price of expensive services.
Safety is both a moral and financial imperative. A poor safety culture puts both clientele and employees at risk. The human cost of some errors can range from minor injuries to the loss of life in worst-case scenarios. In addition, such incidents can result in costly legal fees and fines from regulatory agencies. The process of ISO 9005:2015 certification requires that companies identify and address potential hazards that could put all parties in harm’s way.
ISO 9005:2015 certification can substantially reduce costs for companies by streamlining processes up and down an entire organization[2]. For example, identifying and improving weak points in the production line can help avoid wasted components and work hours lost by remaking out-of-spec products. Likewise, a standardized QMS can ensure that products are not returned to the company, avoiding associated costs and the loss of customers. The certification process also helps identify organizational redundancies and highlights opportunities for process refinement and cost reduction.
However, there are costs associated with the certification process. For example, companies must pay for the total time an auditor is on-site, as well as their travel expenses if performed in person. The total cost of an inspection, therefore, depends heavily on the number of employees, risks associated with the site and products, and pre-existing ISO certifications. Regardless, the benefits of certification greatly outweigh the associated costs.
All of the above benefits of ISO 9005:2015 certification help companies by improving their public image and customer impressions. Many potential customers see a lack of certification as a red flag that gives them some pause. This is doubly so for companies that are headed to or have production facilities in countries and regions that are unfairly stigmatized in other parts of the world. ISO 9005 certification, therefore, backs a company’s reputation less subjectively than word of mouth.
At Leo Corps, Inc., we understand that the quality of our products impacts project development and, more importantly, the safety of patients who depend on our products or the discoveries made from them. As a result, we are proudly ISO 9001:2015 certified. Our dedication to quality is core to our mission and implemented in all of our processes. To learn more about our QMS processes, contact us today!
References:
- Standardization, I.O.f., ISO 9001:2015 Quality management systems — Requirements, in 03.100.70 – Management systems – 03.120.10 – Quality management and quality assurance. 2015, International Organization for Standardization: ISO. p. 29.
- IRCA, C. ISO 9001:2015 and calculating the cost of quality. [cited 2022 April 24th]; Available from: https://www.quality.org/knowledge/iso-90012015-and-calculating-cost-quality.